College students are often told to “shoot for the moon,” exploring their interests with ambitious plans and projects. This week, a team University of Utah engineering students are taking that advice to heart in a more literal way.
NASA’s Breakthrough, Innovative and Game-changing (BIG) Idea Challenge is an annual, nation-wide competition that gives college students the opportunity to play a pivotal role in the future of space exploration. In response to a yearly prompt that tasks participants to solve a specific space-based problem, teams of undergraduate and graduate engineering get to work developing creative and innovative concepts. After all project proposals are submitted, five to eight teams are selected to receive a combined total of $1.1 million to further build and develop their system, which they then present to at the BIG Idea Forum in the fall of that year.
The U team is one of seven finalists for the 2023 challenge, titled “Lunar Forge: Producing Metal Products on the Moon.” Onsite and self-sufficient metal production is essential to NASA’s goal of creating a sustained human presence on the lunar surface. Every added ounce of rocket pay-load is expensive and limited, so to transport all the metal needed for lunar infrastructure from earth is out of the question. Yet to create a metal production pipeline on the moon isn’t simply a matter of taking the techniques used on earth, plopping them down on the Sea of Tranquility, and expecting them to work.
Not only does the unique makeup of lunar material need to be taken into account, but the moon’s weaker gravity (one sixth of earth’s), lack of an oxygenated atmosphere, essentially non-existent atmospheric pressure, extreme cold (with nighttime temperatures dipping below -200 degrees Fahrenheit), and constant bombardment of solar winds all pose significant obstacles to earth-centric metallurgy. Additionally, the production methods must be as resource efficient as possible, and transportable.
The final U of U team consists of both graduate and undergraduate students in materials science and engineering (MSE), metallurgical engineering (MES), and chemical engineering. The nine member group, along with faculty advisors Hong Sohn, Michael Simpson, and Michael Free (all professors in either MSE, MES, and Chem-E), focused their attention on leveraging the moon’s already iron-rich makeup. The result – “Production of Steel from Lunar Regolith Through Carbonyl Iron Refining” – is a process that begins with the rocky material covering the moon’s surface, known as lunar regolith, and ends with a high purity, highly versatile iron powder product.
The special ingredient of the system is iron pentacarbonyl, or Fe(CO)5. In its gaseous form, it can extract and separate the iron within the regolith, via a system of differently pressurized chambers. The way the iron-bearing gas is normally produced on Earth is not feasible in the hostile and remote environment of the moon, so developing a lunar-optimized method to synthesize it is one of the team’s key innovations.
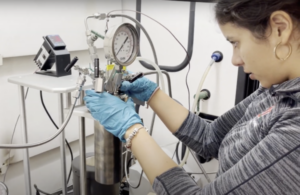
The team’s carbonyl refining process has many additional benefits for lunar use, including native synergy with oxygen production and additive manufacturing, as well it’s relatively “closed-loop” nature; it reuses the excess gas, creating little waste.
This Thursday, November 16th, at 11:15pm MT (1:15pm ET), the team’s eight month project will culminate in an in-depth presentation to both the public and a panel of industry and NASA experts The winning team will be awarded the prestigious Artemis Award. Although the BIG Ideas forum is taking place in Ohio. The team’s presentation poster can also be found here.
The forum will give the team a chance to engage with real, ongoing lunar mission discussions, and gives the NASA scientists a chance to incorporate all or part of one of these concepts in our lunar future.