We’ve been using wood to build things for a very long time. According to the recently discovered remains of a half-a-million-year-old wooden structure in Africa, we’ve been using it before we were even fully human. From those early beginnings, to the stave churches of Scandinavia, to Lincoln’s log cabin, wood as a construction material has been favored for its abundance, its workability, and its beauty.
Yet in the past 150 years, as cities and skyscrapers have boomed, wood has been eclipsed by newer materials such as concrete and steel. These materials are able to support more weight, allowing for bigger buildings, and aren’t as susceptible to fire, earthquake, and moisture damage. At the same time however, they cost more to produce, are not renewable, and extoll a heavy carbon footprint; steel and concrete production accounts for over 10% of global emissions.
But talk to Civil Engineering professor Chris Pantelides, and he’ll tell you that we shouldn’t accept the dominance of the steel-and-concrete jungle just yet. Thanks to the work of engineers like Pantelides, our oldest building material is experiencing a revival — one that can even withstand earthquakes.
Sitting in his office in the Meldrum Building he holds up a block of composite wood, about 12 inches long and 10 inches wide, and smiles.
“What you’re looking at here is the future,” he says.
The deceptively simple piece of lumber is an example of “mass timber” technology, a category of “engineered wood product” set to revolutionize the construction industry— and that Pantelides has spent the last seven years studying and developing.
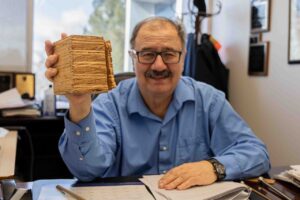
On the desk before him, amongst other pieces of wood and long metal dowels, sits his latest research paper, titled “Design and Cyclic Experiments of a Mass Timber Frame with a Timber Buckling Restrained Brace.”
The paper, authored by Pantelides, his grad student Emily Williamson, and industry researchers Hans-Erik Blomgren of Timberland, and Douglas Rammer of Forest Products Laboratory, was recently published in the Journal of Structural Engineering. It explores the best ways to build a Buckling Restrained Brace — a type of building support that protects against earthquake damage — with mass timber.
As a construction technique, mass timber is defined by its use of columns, beams, and boards made not of a single piece of wood, but of multiple wood layers or pieces tightly laminated or otherwise bound together. The two mass timber types Pantelides works with specifically are mass plywood panel and mass ply lam. These “panelized” or “composite” wood products, as well as their production process, have a number of advantages, environmental and structural, over the usual building materials.
“The timber that we’re talking about, it’s very strong. It can take the place of steel or concrete in many building frames, but it’s much lighter,” Pantelides explains. “A mass timber building is one quarter the weight of a concrete building too, requiring a much smaller foundation.”
Thanks to its super-compressed makeup, mass timber is effectively fireproof as well, resistant to moisture damage, and highly durable.
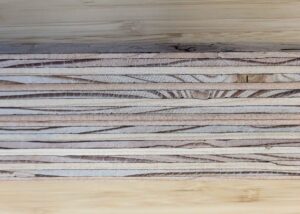
On top of that, with today’s sustainable forestry techniques, using wood is more sustainable and “renewable” than ever.
“It takes only seven seconds for European forests to grow enough timber required for a three bedroom apartment,” Pantelides explains. “Canada alone has enough timber to house a billion people in perpetuity, with forested trees replenishing faster than the population.”
And whereas concrete and steel production is highly carbon intensive, every ton of timber grown sequesters 1.8 tonnes of carbon dioxide from the atmosphere. Further cutting down emissions, and cutting costs, a mass timber building could be 25% faster to build compared to a concrete building, and result in 90% less construction traffic.
According to Pantelides, once the structure is finished the wood goes from benefiting nature to having natural benefits. “People simply like to be in buildings that have lots of exposed wood,” He says. “The sense of being connected to nature, the biophilic design, makes for healthier living and working environments.”
Yet despite all this, steel is still the go to for tall buildings, especially in areas with high risk of earthquakes or hurricanes; steel’s ability to bend and not break under pressure is key. Maintaining a building’s structural integrity relies on a deep understanding of such properties — an understanding we don’t have with the generally stiffer mass timber. This is where Pantelides’ research comes in.
With its varied compositions, mass timber is far from one-size fits all; the type of wood used, the size and shape of the wood particles, how they’re stuck together, or even whether individual layers are stacked parallel or perpendicular to each other will greatly influence how the finished product reacts under stress.
Since he first started investigating mass timber, Pantelides has been troubleshooting and experimenting with different “recipes,” eventually arriving at one that calls for shaving dark fir wood into chips, tightly compressing the chips together into planks or boards, and then laminating those layers together with ultra-strong glue. The resulting plywood can then be securely fastened to other pieces of wood with joints made of steel dowels and plates.
Using this formula, Pantelides and his team began to experiment with mass timber versions of earthquake-resistant architectural elements, including the Timber Buckling Restrained Brace (T-BRB) — the focus of Pantelides’ most recent publication.

In traditional architecture, non-timber BRB’s absorb the seismic force of an earthquake away from the building frame and redirect it to a steel core within the brace, which is usually encased in a concrete-filled steel tube. Instead of a whole buildings’ structural integrity being jeopardized then, only the braces will sustain major damage and need to be replaced. Pantelides’ focus has been to develop a BRB that, while still using a strip of steel for the core, is made of mass timber and tailored for mass timber frames.
That focus requires specialized equipment. Across from Meldrum Engineering Building, in one of the Layton Building’s hangar-like labs, a hulking rectangular metal tower, an actuator, stretches from the ceiling to beneath the concrete floor. The purpose of this gigantic red contraption is to simulate the effects of seismic activity on whatever is placed inside by, basically, vigorously rocking it back and forth. It is here where Pantelides and his team can put “lateral force resisting systems” (LFRS), like the T-BRB, to the test.
He and his grad student Emily Williamson developed several different configurations of this T-BRB before inserting each individually into a timber frame, which was then placed within the actuator. Then: horizontal shaking, and a lot of it— with forces equivalent to a magnitude 7.0 earthquake, for nine tests in total. Sensors attached to the T-BRB and frame recorded how different elements warped or shifted as the test progressed.
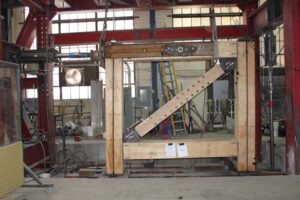
Afterwards the frame and braces were dismantled and further inspected and measured. Pantelides’ recently published paper presents the trove of resulting data, analyzed, graphed, and compared between the different subassemblies. This information will be invaluable in accelerating the use of mass timber construction, allowing it to become tougher and taller.
While mass timber construction has been in use in Europe for several decades now, mostly in regions with low earthquake risk, the US has been slower in adopting it, in part because our strict building codes were focused on steel-and-concrete, treating any use of wood to construct tall buildings with caution.
But now, thanks to recent changes in the language of these codes, along with the type of research that has enabled components like Pantelides’ T-BRB, mass timber is expected to proliferate in even earthquake- and hurricane-prone areas, responding to the increased demand for more sustainable construction materials. The most recent version of the International Building Code, the central set of building regulations in the US, included a construction type that allows the use of mass timber in buildings up to 18 stories. A 25-story-tall hybrid mass timber and concrete building, the new world record, was just built in Wisconsin. Utah now has a large mass timber building under construction in Draper.
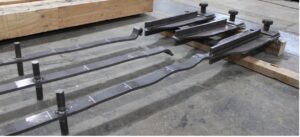
Looking forward, Pantelides is confident in mass timber’s benefits, and the direction the field is heading. It turns out that not only is wood construction in our roots, but it’s our future too.
“The whole world’s waking up! People are going to look back and say, hey, why didn’t we build that with mass timber?” he says. “I think in the next 20 years, there won’t be many buildings less than 12 stories or maybe even 18 stories built with steel and concrete. It just won’t be feasible anymore. In the near future we will even see skyscrapers, over 50 stories tall, that are built using mass timber.”