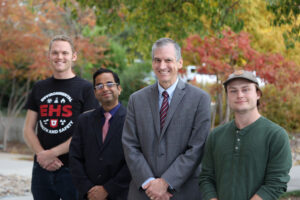
Think about the device you’re reading this on. Whether it’s a smartphone, tablet, or laptop, it contains dozens of rare earth elements and critical metals that make its operation possible. Yet the United States currently relies on foreign sources for approximately 90% of some of these essential materials, creating vulnerabilities in our supply chain for everything from consumer electronics to clean energy technology
The University of Utah is taking bold steps to address this challenge. Mike Free and Prashant Sarswat, metallurgical engineers from the U’s Department of Materials Science and Engineering, have secured two significant funding awards to advance innovative technologies for rare earth elements (REE) and critical metals (CM) processing.
The Defense Advanced Research Projects Agency (DARPA) has awarded $220,446 for developing refined REE and CM products at 90% purity. Additionally, the Department of Energy (DOE) has committed $5 million to support a comprehensive project focused on upgrading mineral resources and optimizing extraction and separation processes to achieve an exceptional 99% purity level for some individual REE and CM products.
“We’re starting with unconventional resources to build a larger supply chain here in the US,” explained Free, principal investigator on the projects and department chair. “We are exploring new approaches that are more environmentally friendly. Some of the technologies we’re developing, like our magnetic separation process, use no additional chemicals, which are very different from conventional processing that can require hundreds of steps and typically involves substantial amounts of acid.”
The research team, which includes graduate students Easton Sadler and Benjamin Schroeder, is developing innovative separation techniques, including a unique device that uses strong magnets to separate rare earth elements based on their magnetic properties. They are also exploring new environmentally friendly extraction methods using specialized materials that can selectively absorb specific elements
Handling the challenge
Sarswat emphasized the challenging nature of their work. “The properties of rare earth elements are so similar that existing methods and technologies are not very effective at separating them. With our methods, whether it’s magnetic or physical separation or adsorption, we can handle that challenge,” he said.
The U is one of only two institutions selected in this competitive second DOE funding round, alongside Caltech. The project team includes collaborators from Virginia Tech and has secured crucial industrial partnerships for commercialization.
The research aims to produce:
- Five individually separated, high-purity rare earth oxides/salts at ~90-99.99% purity
- Five individual or binary rare earth metals at ~99.5-99.8% purity
- Five additional ~90-99% pure individual critical metals as oxides, salts or metals from coal byproducts
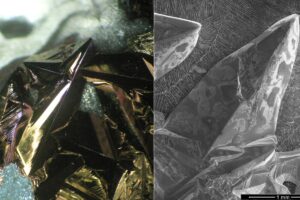
Ben Schroeder and Easton Sadler’s application and improvement of groundbreaking techniques for separating rare earth elements—essential materials for advanced technologies like high-performance magnets and precision lasers—are complementary. Schroeder’s approach harnesses the magnetic properties of rare earth elements, using powerful magnets to create a sophisticated separation process.
“We have a solution with multiple metals, and we want them to not be mixed together,” Shroeder explained. By flowing the solution over strategically positioned magnets, he creates concentration gradients that physically separate elements based on their magnetic susceptibility. Rare earth elements that are more magnetically responsive get pulled into specific channels, while less magnetically responsive elements continue to flow, resulting in increasingly pure elemental fractions.
Sadler takes a chemical approach in the lab, to develop more environmentally friendly extraction methods than the industry standard. “The state-of-the-art now uses organic solutions and acid, which are expensive, corrosive, and toxic,” Sadler noted. He’s designing innovative solid materials coated with specialized extractants, like graphene and trimesic acid, that can selectively capture specific rare earth elements. Through iterative experimentation, Sadler is working to create materials that can withstand acidic environments while efficiently separating elements.
Continue reading David Pace’s “Purity at a premium in critical metals” at the College of Science.