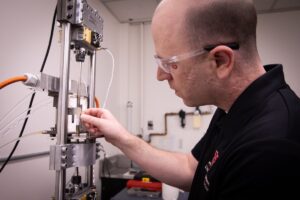
For mechanical engineers interested in the way things fall apart, “creep” is as scary as it sounds. Creep is the term used to define the gradual process of materials changing shape when exposed to persistent forces for long periods. As the name suggests, creep happens so slowly it is imperceptible to the naked eye, but it can eventually cause failure.
Mechanical engineers need new tools to study the fundamental mechanisms governing creep behavior in novel material systems, especially if they want expedite experiments with the goal of obtaining results in days rather than decades. That’s where the University of Utah’s new Psylotech Micro Test System (μTS) comes in.
Housed in the lab of Mechanical Engineering Associate Professor Owen Kingstedt, the system is known as a “load frame” — it can precisely “load” samples of a material with physical forces under highly controlled temperatures. The controlled conditions of the load frame enable surrogate experiments, which replicate the extreme environments experienced by materials in energy, aerospace, and defense applications where premature failure is not an option.
For decades, researchers have relied on long-term experiments to study how materials degrade under constant load. Japan’s National Institute for Materials Science, for example, maintains a vast database with results from experiments that have run for over 20 years. While valuable, such extended timelines needed to obtain quantitative understanding make it difficult to rapidly assess new materials.
“If these experiments are going to take multiple years, we want to know more about their likelihood of success before we begin,” Kingstedt says. “The load frame helps us perform surrogate experiments to forecast possible results in days or weeks so we can make informed decisions at the outset of an experimental campaign.”
The Psylotech system’s capabilities will support nuclear reactor development by improving the identification of new candidate alloys that demonstrate the capacity to withstand decades of heat and pressure.
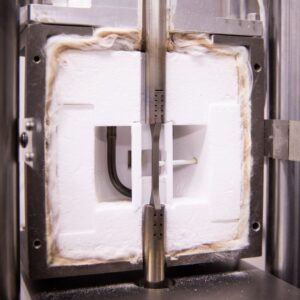
The Psylotech system offers a solution by accelerating creep experiments through its ability to manipulate temperature on the fly. The system can test materials under temperatures ranging from -100°C to 1,600°C — a range ideal for simulating extreme conditions found in next generation nuclear reactors, as well as in various aerospace and defense applications.
“This is a unique piece of equipment,” Kingstedt says. “We’re the only academic institution in North America with one.”
The University of Utah is now even better positioned to collaborate with institutions like Idaho National Laboratory, to support next-generation reactor designs and other advanced engineering projects.
This new equipment goes beyond studying creep. The Psylotech system eliminates the need for multiple machines to perform different tests. “Usually, you take a specimen to one load frame and run a tension test, then you go to a different machine to run a fatigue experiment, and a different one to run a creep experiment,” Kingstedt explains. “The Psylotech can do all three. It is the Swiss army knife of the lab.”
The system’s compatibility with digital image correlation (DIC) techniques presents another significant advantage. DIC techniques use high-resolution images to track material deformation with extremely high precision, giving researchers valuable insights into how materials respond under extreme conditions.
The equipment’s versatility also extends to aerospace applications.
“In aerospace applications, we’re looking at materials that face extreme thermal and mechanical loads—rocket nozzles, jet engines, components that operate continuously at thousands of degrees,” Kingstedt says. “With this system, we can quickly test different material compositions so we can screen potential candidates much faster and refine them long before they ever go into a real-world system.”
“With this system, we can test materials in ways that weren’t possible before. It puts us in a position to lead the way in advanced materials research,” Kingstedt says. “This gives University of Utah researchers the chance to accelerate discoveries that could otherwise take decades.”
The acquisition of the Psylotech Micro Test System was supported by a Department of Energy nuclear infrastructure initiative.